コラム
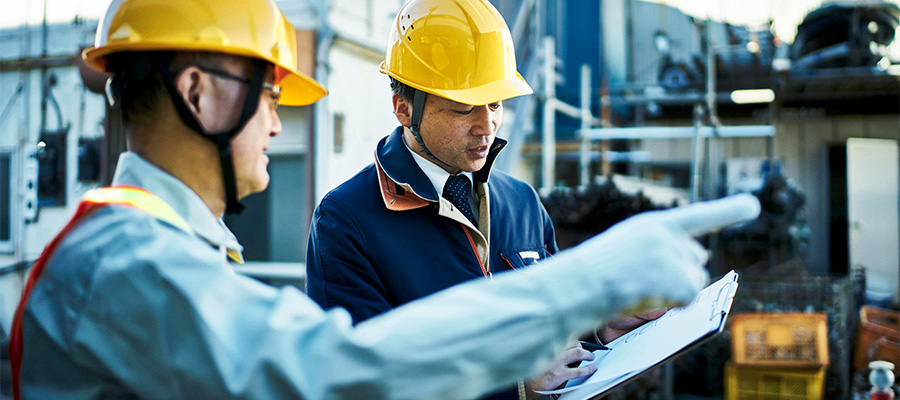
厚生労働省労働局長登録教習機関
北海道・宮城県・岩⼿県・福島県・東京都・⼤阪府・福岡県
作業場で行う安全活動として、KYKまたはKYTというのは、一度は耳にしたことはあるのではないでしょうか。
KYとは、危険予知のことで、危険の「K」と予知の「Y」の頭文字を取って、KYです。
KYKは危険予知活動、KYTは危険予知トレーニングの略になります。
本文では、KYで統一します。
KYは、作業場や作業に潜む、安全意識の高揚や危険に対する感受性を高めて、起こりうる危険に対処することを目的とした活動です。
つまり、現場で行う安全活動のことです。
KYの主体は、事業者ではありません。作業を行う人になります。
多くの場合、作業前に作業リーダーが中心となって、ミーティングとともにKYも行うというケースは多いのではないでしょうか。
このKYは、今から行う作業にはどんな危険があり、どのように対処していけばいいのかということを、明確化するのには、大変意味がある活動です。
現場においては、実地に則した、安全教育であるとも言えます。
KYを行うことによって、各作業員が危険を意識し、危険への対処法を考え、予防する。
とても理にかなっていますし、うまく機能すれば、とても有用です。
しかし、一方で課題もあります。
今回は、そんなKYについてです。
KYは現場単位、作業単位で行われる安全活動です。
製造業、建設業、運送業などに限らず、取り入れられているところは多いと思います。
やり方などは、大体共通していると思いますが、まずは大まかな流れをまとめます。
ここで紹介は、KY講習などで教えられている「KY4ラウンド法」です。
こんなKYはやっていないという事業所もあるでしょうが、それはそれで問題ないです。
一応、4ラウンド法は、中央労働災害防止協会などが勧めている方法であり、可否があるわけではないのです。
何より、やっている内容は、さほどずれていないと思います。
それでは、KY4ラウンド法です。
1R 「どんな危険が潜んでいるか」
作業の中に潜んでいる危険を想定し、考えられるだけ全て洗い出す。
2R 「これが危険のポイントだ」
発見した危険に、特に重要だと思われるものを選ぶ。
みんなで話し合い、1つに絞り込こむ。
3R 「あなたならどうする」
最重要の危険への対策方法を出す。
4R 「私達はこうする」
対策の中から、全員で実践する方法を決め、重点実施事項とする。
重点実施事項は、チームの行動目標とし、確認のため、全員で指差呼称する。
これが、一般的な4ラウンド法の流れです。
紙に書いて行う場合は、2Rの最重要の危険に◎印をつける、4Rの重点実施事項に※印をつけるなどがありますが、そういったものは割愛しています。
仮に4ラウンド法をやっていないという事業所でも、「危険は何か」と「対策法」という形で実施されているのではないでしょうか。
さて、この4ラウンド法ですが、1Rでお勧めされているのは、作業方法や現場のイラストシートを見せて、話し合うというのが基本です。
ところで、KY講習を受けた時にも思ったのですが、こう問いたい。
誰がそのイラストを書くのだと。
誰がそのイラストを準備するのだと。
全作業のイラストについて、KYをやるのかと。
仕事は他にもあるが、イラストに描かれた仕事以外の場合は、無視かと。
講習では、この疑問が解決しないまま、終わっていきました。
一方で、KY用のイラスト集は販売されています。
しかしそれは、実際の作業に則しているのかというと、必ずしもそうではありません。
作業は千差万別。
それに対応することなど、不可能なのです。
そのため、とりあえずイラスト云々は置いておきます。
この4ラウンド法ですが、基本的な流れについては、わかると思います。
どんな危険があるのかを考え、その対策を考える。
さらに危険は全て一様ではありませんよね。
段差で足を引っ掛ける危険と、高所作業中に足場から足を踏み外して墜落する危険とでは、どちらの危険をより中止しなければならないかは、明白だと思います。
これが危険対策の優先順位をつけるということです。
本来ならば、全ての危険に対して、万全に注意するのが理想ではあります。
もしかすると、考えれれる危険は全て対策すべきだという意見もあるかもしれません。
しかしながら、これは現実的ではありません。
なぜなら、人の記憶には容量があり、何もかも覚えていることなんてできないのです。
しかも作業をしながらですから、KYの内容などすぐに頭から抜けてしまいます。
そのため、優先度が高いものを1つに絞り込み、この1つだけはしっかりやろうということなのです。
高所作業で足場を使う時は、足元への注意を行うこと。
これだけ頭に叩き込み、重大災害を予防しようということなのです。
とても理にかなっているようですね。
ただし、きちんと理想通りに機能すればですが。
さて、私の思うKYの課題についてですが、これが理想的なやり方だという提示はありません。
私の会社でもKYを行っているものの、あれこれ試行錯誤です。
その中で、現在試行している方法は示したいと思います。
1つ目の課題は、「形だけになっていないか」です。
4ラウンド法などもですが、KYは書くことを想定しています。
社内の安全管理体制がしっかりしている会社や、建設業ではKYは作成しなければならない書類の1つだと思います。
私の会社も建設業ですが、KYは毎日記入し、竣工時の検査書類の1つとして求められています。
形だけになっていないかというのは、実施云々ではなく、ただ書類として作っているだけのものではということです。
自発的であろうと、指示による強制であろうと、実施するのが重要という意見もあるでしょう。
これも一理あります。
一方では、当初の目的とはかけ離れ、手続きにだけになっている面もあるということです。
この背景には、書類主義的な社会体質もあるのでしょう。
市役所等での手続き、ショップで携帯電話の機種交換をする時などを想像してみてください。
毎日の作業現場でも同様のことが起こっているです。
当然、作る側はうんざりします。
管理側は書類を多く求める、実施側は書類を作るのは手間がかかるので、減らしたい。
KYが書類として作るものだけにしているのは、このような背景があるのかもしれません。
もう1つの背景は、KYの目的や効果などを、作業員が理解していないというのもあるかと思います。
雇入れ時の教育で伝えているのかもしれませんが、他にも覚えることがあれば、忘れてしまいます。
そのため、作業リーダーが、全作業員にKYの意義を伝える体制も重要ですね。
2つ目の課題は「マンネリ・ネタ切れ」です。
仕事の内容は事業者ごとに千差万別です。
このような台詞もよく耳にします。「うちの会社は特殊だから」。
確かに体制や仕組み、仕事のやり方は特色があるのでしょう。
しかし、1つの会社で行う作業そのものは、さほどバリエーションがあるわけではありませんよね。
いくつかのパターンに収まり、それから外れることは少ないと思います。
特に製造業であれば、プレス機担当はプレス機操作を、組立担当は組立作業をと、大体決まった仕事を行うのが常ではないでしょうか。
建設業は、現場ごとに仕事の内容は違いますが、作業内容は掘削、運搬、コンクリート工など、大体パターン化されます。
また鉄筋・型枠組立、足場組立など、会社ごと特化しているもあるので、仕事の内容は限られたパターンになります。
同じパターンの仕事を繰り返すことで経験を蓄積していき、どのような状況でも仕事ができるようになっていくわけです。
仕事の内容がパターン化されているのですから、起こりうる事故や危険もパターン化されるわけです。
プレス機の仕事であれば、金型の間に指を挟まれるの危険があり、対策も指を入れないや、もし入れる場合には必ず電源を切る等になります。
これは日ごとに変わることはなく、常に最重要の危険になるわけです。
高所作業であれば、墜落の危険があり、対策としては足場の手すりの確認や安全帯着用があります。
これも高所作業を行う限り、常につきまとう危険です。
こういった場合は、KYは常に同じ内容を書き続けることになります。
同じ内容を書き続けるのは、飽きます。
このワンパターン、マンネリ化は、KYでもたらされるはずの危険への感受性も鈍らせます。
これは毎日行うので、仕方がないのかもしれません。
飽きてしまうと、重要度は下がります。
これも手続きだけのKYにしてしまっている要因なのかもしれませんね。
このような課題もありますが、KYは少人数でできる安全活動です。
その日その日の作業の中で、特に重要な危険と安全対策に注意を向けることは、事故予防のために重要です。本人だけでなく、周囲の人も注意することができます。
作業はいくつかのパターンになるわけですが、今私の会社では、KYシートを工夫し、過去の作業写真からいくつかピックアップして、イラスト代わりにしています。
このシートを作業の種類ごとに用意し、KYで使用してもらっています。
これが効果があるかは、検証中ですので、現時点では効果があるとは言えないですけども。
参考までに、サンプルとフォーマットを載せてみます。
サンプル
フォーマット
KYはよく耳にするし、やっているけど、ただやっているだけから脱却するには、何のためにやるかを明確化することです。 これは、事業者や作業リーダーが中心になって、全作業員に啓発していく必要があります。
さて、最後にKYとリスクアセスメントは、手続きの流れだけ見ると違いがないように見えます。
リスクアセスメントも、まず危険を洗い出し、優先順位をつけ、対応策を検討します。
KYの流れと同じようですね。
この両者の違いは、リスクアセスメントは設計段階、または機械設置、材料変更などの作業方法の変更時に行う抜本的な安全対策のために行うものなのです。対応は1個人ではなく、全社的に行います。
一方、KYはこれらリスクアセスメントで対応しても、漏れてしまう危険に対するものです。
リスクアセスメントで対応しても残留する作業時の危険、または各作業員の行動に起因する危険、つまりヒューマンエラーなどへの対策です。
つまり、とても簡単に違いを言うと、段階と対応する規模が異なるということです。
もちろん目的は、どちらも災害予防なのは違いありません。
一応リスクアセスメントとの違いも必要かなと思ったので、補足してみました。
考えようによっては、ネタ切れ、マンネリ、ワンパターンでも構わないと思います。
愚直に、最も重要な危険対策を行い、予防し続けられているならば効果ありです。
書類を出す目的だけになっているのは、ちょっと考えものですが、これは書類重視の社会なので、どうしようもないのかもしれません。
しかし形はどうであれ、結果として労災予防になれば、良しです。
最も大切なことは、1日怪我なく、病気なく、仕事を終えるということです。