コラム
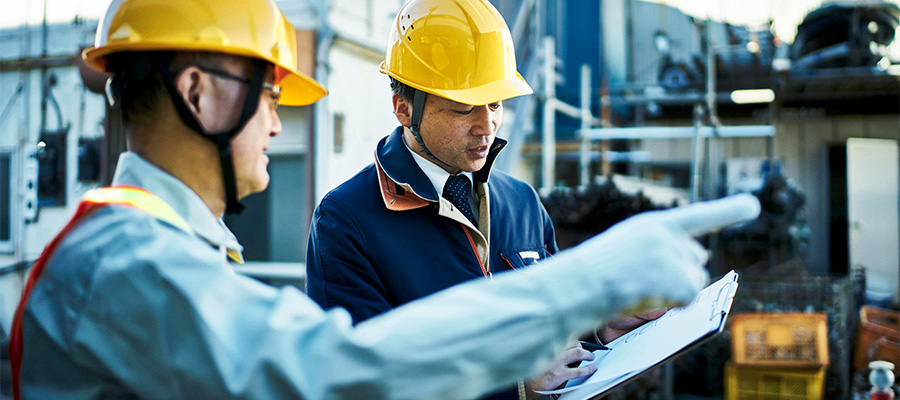
厚生労働省労働局長登録教習機関
北海道・宮城県・岩⼿県・福島県・東京都・⼤阪府・福岡県
機械とともに行う作業は、危険を伴うものですが、通常さほど危険があるわけではありません。
機械には安全装置があるため、接近し過ぎることを防ぎます。
作業には際しては、適切な手順で行われます。
通常の作業中は機械と人とは、適度な距離を保たれ、安全です。
しかし通常の作業ではなくなった場合、その距離感が安全なものでなくなります。
機械と人が接近し、接触する時、それは修理や点検、メンテナンスの時です。
修理などでは、遠隔で行うことは困難です。
どうしても、直接触らなければなりません。
もし直接触っている時に、動いてしまったら。
挟まれたり、巻き込まれたりしてして大事故になってしまいます。
こういった機械の誤作動による事故を防ぐためには、電源を落とすことで防ぎます。
しかし、電源が入っていなくとも、修理中に事故になってしまうこともあります。
それは、機械そのものが襲い掛かってくる場合です。
機械は金属の固まりです。その重さは、数百キロ、数トンになります。
それが襲いかかってきたら、人の体では、太刀打ちできません。
自動車メーカーのスズキの工場で、機械の修理中に事故が起こりました。
この事故により、1名の方が亡くなられてしまいました。
今回は、この事故の原因を推測し、対策を検討してみます。
スズキの工場、鋳型と機械に挟まれ社員死亡
(平成27年3月19日)
21日午後11時頃、静岡県掛川市西大渕のスズキ大須賀工場で、自動車のエンジン部品の鋳型を製造する機械がずれ、元の位置に戻そうとした同社社員が、出来上がった鋳型と機械の隙間に挟まれた。
被災者は病院に搬送されたが、まもなく死亡が確認された。 同社と掛川署によると、被災者さんは、別の男性と機械を戻そうとした際、何らかの原因で挟まれたという。同署が詳しい事故原因を調べている。 |
読売新聞(元の記事が削除されているようです。)
この事故の型は「はさまれ」で、起因物は「工作用機械」です。
作業中でしょうか、機械の一部がずれてしまい、そのままでは仕事ができなくなりました。
仕事を続けるためには、機械を元に位置に戻さなければなりません。
被災者は、機械をストップさせ、直ちに機械を元の位置に戻そうとしました。
しかし、事故はそんな時に起こったのです。
機械をストップさせたのですから、すぐ側には完成した部品がありました。
被災者は、機械と製品との間に入り、機械の位置を戻そうとしていた時です。
機械が被災者に向かって来ました。
避ける暇もなかったのかもしれません。また避けようとしたけれども、すぐ側にあった製品に邪魔されたのかもしれません。
事故は起こってしまいました。
なぜ機械がずれてしまったかなどの、直接的な原因については、調査中なので、今後明らかになっていくでしょう。
実際のところは分かりませんが、機械の位置を直す作業は1人で行っていたのかもしれません。
また作業中に機械がずれてしまうということも、日常的によくあったことだったのかもしれません。
鋳型は少しずれただけでも、使い物にならなくなるので、ほんの少しのズレも許されないものです。
繰り返し作業を行っていると、どうしても修正が必要になるはずです。
被災者に向かって、滑り落ちたということですから、固定物が完全に外れたと思われます。
作業手順に問題が合ったのか、手順通りだったけれども問題が起こったか、今後調査されていくと思います。
それでは、記事からでは情報が少ないですが、原因を推測してみます。
1.機械の位置を直そうとした時に、機械が落ちてきたこと。
2.安全ブロックなど、落下防止対策をとっていなかったこと。
3.作業を避難できない位置で行ったこと。
4.作業手順が適切でなかったこと。
スズキの工場ということもあり、作業手順が定められていなかったとは考えにくいです。
確かなことは分かりませんが、作業手順は定められていたことでしょう。
作業手順があったとしたら、安全ブロックを使用することなどの、安全を確保する手順が定められていなかったか、手順を無視したかなどが考えられます。
いずれの理由かは、分かりませんが、作業中に十分に安全対策が取られていなかったことは、確かのようです。
仮に固定が困難と思われる場合は、別の作業者に協力が得られたら、違った結果だったのでは思われます。
対策を検討してみます。
1.機械の固定を確保する措置をとる。
2.安全ブロックなどの、落下防止対策をとる。
3.作業場所は、安全が確保される位置で行う。
4.作業手順を見直し、作りなおす。
作業手順が適切だったのか、作業手順通りに作業を行ったのかが、ポイントになります。
しかしいずれにせよ、このような事故が起こってしまったのですから、作業手順に問題があったと言えるでしょう。
今後見直しが行われ、再発防止に努められることだと思います。
作業手順というものは、一度作れば終わりではありません。
当然ですが、抜けているところや、実際にやってみたらうまくいかないことなどがあります。
安全ばかりを重視すると、効率が悪くなります。
逆に効率重視だと、作業者に危険を及ぼしかねません。
バランスが大事です。
最初から安全と効率をバランスよく手順に盛り込むことは、まず不可能でしょう。
実際に行いながら、フィードバックを受け、改善していくしかありません。
当初想定していなかったけどれも、重要なポイントなども、作業していて見つかることも多いです。
定期的に見直しを行うことが、大事なのです。