コラム
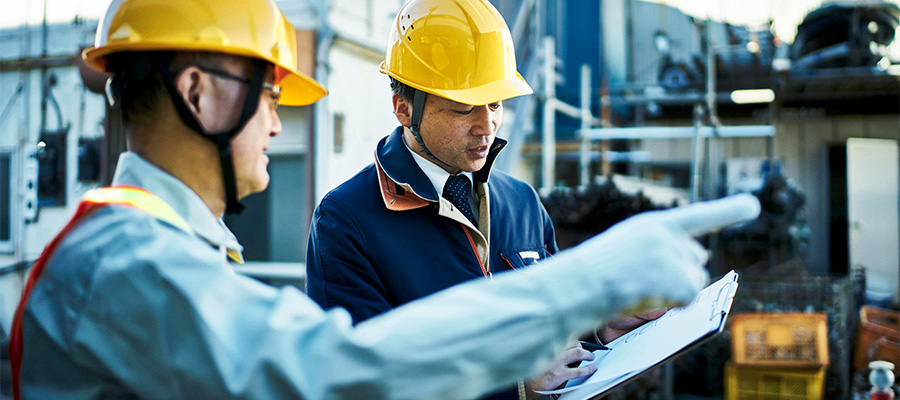
厚生労働省労働局長登録教習機関
北海道・宮城県・岩⼿県・福島県・東京都・⼤阪府・福岡県
「3Mをなくすために、5Sを徹底する。そしてそのために重要な事は、1つのCだ。」
こんな台詞を聞いたのですが、何を言っているのかわかるでしょうか?
それぞれの用語を知っていれば、何となく察しはつきますが、そうでなければ、DAIGO風に言うとMWW(まじで訳わからん)という感じです。
ビジネスでは横文字が溢れており、中には頭文字を使った略称になっているものもあります。
その1つが、4Sや5Sでしょう。
4Sとは、「整理」、「整頓」、「清掃」、「清潔」の頭文字をとった、品質や安全活動のことです。
5Sになると、これらに「躾(しつけ)」が加わります。
ちなみに、冒頭の3Mとは「ムリ」、「ムラ」、「ムダ」のことで、1つのCとは「コミュニケーション」のことを指します。
そう言われていみると、何となく筋が通りますね。
製造業の拠点が、海外に移り久しくなります。
国内の工場は縮小、統合、閉鎖され、多くの製品が中国や東南アジアで作られています。
理由としては、生産コストの効率化がありますが、工場1つが失われることは、その工場に勤めていた数百人の雇用が失われることも意味します。
品質は確保しつつ、価格競争に巻き込まれ、コスト削減を迫られる中で、国内での生産活動で黒字を出すことは、至難の技です。
しかし絶大なる努力により、売上が半分になっても、黒字化を実現する工場もあるようです。
生産活動の効率化で、指標となっているのはトヨタではないでしょうか。
徹底した効率化は、他社の参考となっています。
トヨタ式に代表されるように、各工場でも作業の効率化、低コスト化を実現するため、日々努力されています。
そんな努力をされている会社に、リコーがあります。
先日、リコーの5S活動ということで、話を聞く機会がありました。
少しその話をまとめてみます。
リコー系列であるリコーユニテクノ(株)(2013年4月をもって、リコーテクノロジーズ(株)とリコーインダストリー(株)に分社、統合化)はFAXやコピー機を製造をしています。
90年代半ばに、リコー本社はFAX等の生産拠点を中国とする方針を決めました。
その決定は、リコーユニテクノは困らせました。
なぜなら、生産の大半を外部にとられ、この数年で売上が半減するからです。
このままでは閉鎖せざるを得ない。
社員たちも辞めざるを得ない。
そのような危機的状況から、いかに会社と社員を守るのか。
生存を掛けた、挑戦が始まったのでした。
工場が独自で新製品を開発するという選択肢はありませんでした。
できることは、今ある製品の生産と売上が半減しても、耐えられるようにすることです。
やれることには制限があります。
自分たちでできること、やれることというのが、作業の見直しと効率化でした。
まずはムリ、ムラ、ムダの3Mの洗い出し。
仕入れ、運搬、組み立て、廃棄物までありとあらゆるものを見直し、チェックし、改善していきました。
作業者自身でできる改善として、動作のムダの改善でした。
製造ラインでの作業は、最終的に製品を生み出すのですが、実は生産に関わる仕事というのはごく一部でしかありません。
例えば、流れてきたパーツを、ドライバーでネジ締めするという過程があったとします。
この場合、作業は次のとおりになります。
1.材料を受け取る
2.工具入れからドライバーを取り出す
3.ネジを締める
4.材料を次工程に流す
5.ドライバーを片付ける
常に全ての作業を行うわけではないのですが、生産活動に関わる作業はどれか?
答えは、3の「ネジを締める」のみです。
その他の作業は、3のための補足作業になります。
3以外でのロスをなくすための見直し。
これが作業のムダを無くすことです。
作業のムダとは、動作のムダとも言えます。
動作のムダには、次の種類があります。
・片手が遊ぶ
・両手が遊ぶ
・歩行する
・振り向き動作が大きい
・ながら作業
・背伸びする
・腰をかがめる
・持ち替える
・カンコツが分かってない
・作業動作そのもの
他にも2、3個あったと思いますが、忘れてしまいました。
製造業の現場で、今や当たり前なのでしょうが、1秒のムダを無くすなんて、こんなことまでするのかーと驚きです。
窮屈そうな気もするのですが、そうでもないのでしょうか?
とはいえ、これらの改善により、リコーユニテクノ(現リコーインダストリー)埼玉工場は2000年代半ばには、黒字転換し、今では工場見学が3ヶ月待という状況だそうです。
時として、常軌を逸することもある改善活動。
リコーは、うまく効率化をはかれた例でしょう。
ムダをなくすということは、今の作業全てを一度、疑うことから始まります。
本当に、ドライバーはこの道具箱に入れていていいのか?
道具箱は、この形でいいのか?
右手の位置はこれでいいのか?
作業台の高さはこれでいいのか?
などなど、一挙手一投足に光を当てる必要があります。
作業の効率化と質を高めるのに、効果的なのが5Sでもあります。
ムダなものを排除する整理、取り出しやすいように収納する整頓、清掃し、清潔にする。
そして、全員が行うようにする躾です。
リコーでは、さらに3Sを加えて、8Sとしているそうです。
3Sには、「しっかり」、「しつこく」、「しんじて」だそうです。
これは精神論なので、5Sとは意味合いが違います。これくらいの気持ちでというものでしょう。
5Sの徹底は、事故防止になります。
製造業では、多くの機械や材料に囲まれた環境のため、危険がいっぱいです。
整理整頓により、危険の芽を積んでおく。
これが事故を防止にすることになります。
製造業で最も深刻な事故は、機械などへの「はさまれ・巻き込まれ」です。
しかし見落としがちですが、事故として多いのが、転倒です。
転倒で大怪我?と思うかもしれませんが、骨折など深刻な被害が出ることも少なくありません。
4S、5Sは転倒事故防止になります。
転倒防止のために、沖縄労働局では、作業場の転倒危険チェックシートというものを公開しています。
職場の危険箇所などをチェックするのにも使えるので、ぜひご活用ください。
作業の見直し改善は、危険箇所の発見にもつながります。
1つの作業には、本人も気づかぬムダと危険が潜んでいます。
工場作業を見直すのは、どこでもやっているというのはあるでしょうが、成功例を参考にして、自社の改善に取り組むのも、今後生き残る道でしょう。
とはいえ、劇的に変化を求めると失敗します。
人とは変化に弱く、抵抗を感じます。
ダイエットを失敗するのも、痩せた状態へ変化することに、心理的な抵抗を感じてしまうからです。
変化はほんのちょっとずつです。
例え角度にして1°の変化でも、時間が経つと、大きな差になります。
そして、変化するときに、絶対疎かにしてはいけないのは、安全です。
効率化の結果、作業者が危険にさらされる、体の負担が増えるといったことでは、本末転倒も甚だしいです。
安全が確保された上での、効率化であることは、ぜひ肝に銘じてもらいたいものです。